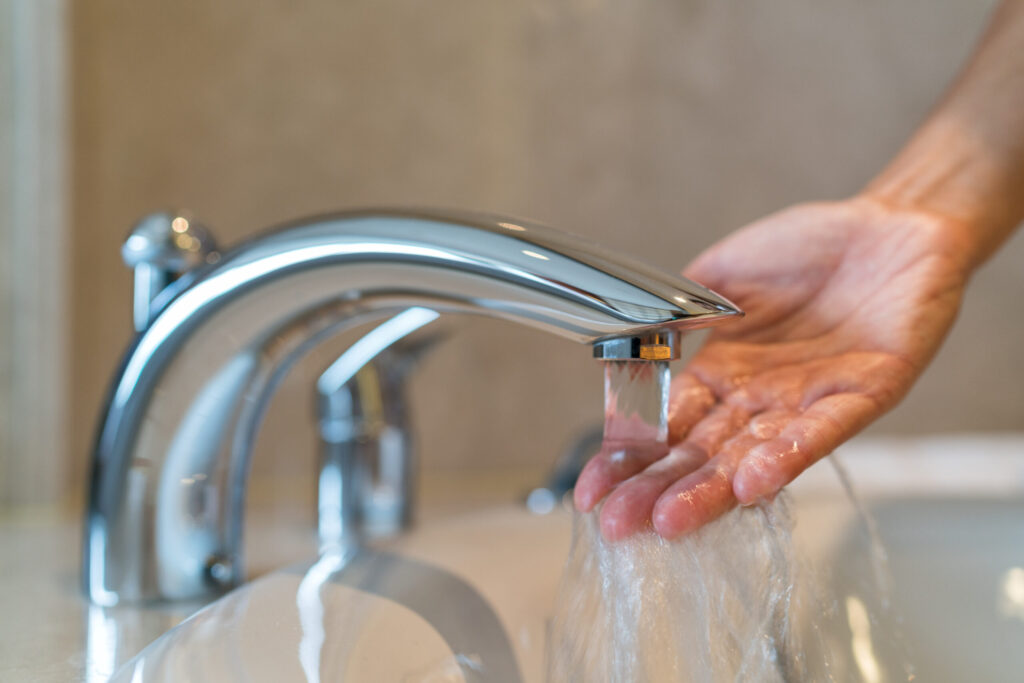
A home feature often seen in new construction are recirculation pumps, allowing for faster hot water response times to sinks and showers, especially when the fixtures are located a far distance from the water heater. Although including a recirculation pump is a common practice by homeowners and builders, many are not aware of the Energy Code implications. If a recirculation system is not accurately shown in the drawings and Title 24 report, the HERS Rater or Inspector may discover the issue on site, leading to unfortunate field corrections.
Demand-control Recirculation allowed prescriptively
A recirculation distribution system is allowed prescriptively but it requires a demand recirculation control. Demand control minimizes pump operation and heat loss from pipes, versus continuous recirculation or even recirculation on a timer. There are two types of demand control, a Manual control (often called a push-button) and a Motion Sensor control (typically in the fixtures).
The following are installation criteria for a Demand Control Recirculation system.
- Pump start up must be provided by a push button or occupancy sensor.
- Pump shut off must be provided by a temperature sensing device when the sensor detects no more than 10-degree rise above the initial temperature of water in the pipe or when the temperature reaches 102 degrees F. The controls also must limit the maximum pump run time to five minutes or less.
- Piping in a recirculation system cannot be run up to the attic and then down to points of use on the first floor.
- Push buttons or sensors must be installed in all locations with a sink, shower, or tub, with the exception of the laundry room.
- Plans must include a wiring/circuit diagram for the pump and timer/temperature sensing device and specify whether the control system is manual or other control means.
Additional Options under the Performance Method
Project teams can utilize a different hot water distribution system under the Performance method, which could provide a Credit or Penalty for Title 24, depending on the system selected and whether HERS verification is included.
The following table outlines all available recirculation types and the credit or penalty multiplier associated with each. The baseline is ‘Trunk and Branch – Standard’ with a multiplier of 1.0. The baseline does not include a recirculation pump. The other systems are compared to that baseline with a multiplier indicating if that approach would be a credit (lower than 1.0) or penalty (higher than 1.0).
A few items to note:
- ‘Non-Demand Control Options’ has a penalty of 9.8, which is huge and would typically be enough on its own to fail a home’s energy compliance. In other words, a home can include a recirculating system that runs continuously or on a timer, but the rest of the home would need exceptional energy efficiency in other areas to make up for it.
- ‘Recirculation with Manual Demand Control’ has a penalty of 1.75, which is still a penalty but easier to balance away from with other home features.
- Most of these solutions offer a HERS Verified version as well, which provides better credit (or less of a penalty) but, of course, would require having a HERS inspector verify installation and operation.
Table 5-9: Applicability of Distribution Systems Options within a Dwelling Unit (excerpt)
Distribution System Types | Assigned Distribution System Multiplier – NO HERS | Assigned Distribution System Multiplier – WITH HERS |
Trunk and Branch – Standard (STD) | 1.0 | n/a |
Recirculation: Non-Demand Control Options | 9.8 | n/a |
Recirculation with Manual Demand Control | 1.75 | 1.6 |
Recirculation with Motion Sensor Demand Control | 2.6 | 2.4 |
Other DHW strategies are available
When using the performance method, an efficient distribution system can improve compliance margins significantly, especially in climate zones 4-9 where water heating represents a large fraction of the energy budget.
In addition to the recirculation options, there are four other distribution approaches that could impact a performance method of compliance for the hot water section of Title 24.
Table 5-9: Applicability of Distribution Systems Options within a Dwelling Unit (excerpt)
Distribution System Types | Assigned Distribution System Multiplier – NO HERS | Assigned Distribution System Multiplier – WITH HERS |
Trunk and Branch – Standard (STD) | 1.0 | n/a |
Parallel Piping | 1.1 | 1.0 |
Compact Design | 0.7 | 0.3 – 0.7 |
Pipe Insulation | n/a | .85 |
Point of Use | .3 | n/a |
- Parallel Piping uses a loop tank piped in parallel with the primary storage.
- Compact Design is based on measurements to calculate a ‘weighted distance’ to where the hot water is used. The closer the better in terms of the multiplier, and more credit is available when verified by a HERS Rater.
- Pipe insulation is already required, but a credit is available when the installation is verified by a HERS Rater.
- Point of Use offers the greatest available credit for hot water distribution. Note that a point of use system must have the water heater and any fixture using hot water be within the lengths specified in Table 5-10.
Table 5-10: Point-of-Use Distribution System
Size Nominal, Inch | Length of Pipe (feet) |
3/8″ | 15 |
1/2″ | 10 |
3/4″ | 5 |
Hot water and happy residents
In general, people like having hot water available quickly without wasting cold water down the drain or letting hot water ‘cool off’ when it’s recirculated without use. With the options and requirements for hot water distribution in single family homes, the energy code is balancing the need to save energy and water with the public’s interest in having hot water there when they want it.
For more information and in-person trainings, please check out our events calendar at 3c-ren.org/calendar-of-events-and-trainings
The on-demand webinar page is at 3c-ren.org/on-demand-trainings
And feel free to reach out to the Code Coach Hotline for more information or to have your Energy Code or CALGreen questions answered! 3c-ren.org/energy-code-coach